Do you know the term “Bus Factor”? This concept is more well-known in the IT industry, and I think it will be increasingly used in the construction industry over time. Why? Because we are increasingly programming and automating projects to make our lives easier.
Bus Factor is a measure of risk resulting from a lack of sharing information and skills among team members. In simplified terms, it is the number of people who would need to be “run over by a bus” in order for the project to become impossible to continue. Of course, this should not be taken literally, but rather understood that the Bus Factor refers to any random event that could cause a key person in the project to disappear, and as a result, the project would be unable to continue or introducing a new competent person would be very expensive and risky.
This post was written by BIM Corner’s Guest Author, Magdalena Niemiec.
In the IT industry, to prevent such situations, a project is divided into a greater number of tasks with smaller scopes. And more people are involved who try to ensure that others know exactly what each person is doing on the project. It is also a good practice to use a Guidebook, which is essentially a project guide. You will find good practices used in programs – problem-solving instructions that arise from project to project and are typical for a given industry and project. The Guidebook aims to systematize work and prevent reinventing the wheel.
This article will explain why it is worth creating Standards, Procedures, and Guidebooks in a design office or a construction company and what such a document should contain. Below are brief descriptions of the differences between each of these documents.
Table of contents
Policy [Strategy], Standards, Procedures [Requirements], Guideline [Guidelines] - PSPG
Have you ever experienced a situation where during a two-week absence of a colleague, you had to “jump in” on a project to replace another team member and waste a whole week getting familiar with the program and project information? The typical question in such a case is: “What and where can I find it, and why was it designed this way?” It sounds like a nightmare, doesn’t it? However, for people on the other side who know they will face chaos when they return from their “break,” it is also an uncomfortable situation that causes feelings of guilt, worse recovery, stress, etc. These are situations that unnecessarily build tension, and personally, I believe that if we can prevent such events, why not do so for everyone’s comfort?
To avoid employee frustration, save project budgets, and facilitate the onboarding of new or temporary employees on a project, standards, procedures, and guidelines are used. Many of you may have encountered these terms, but we often use them interchangeably or inappropriately.
In short: policy is a unified high-level declaration (given by the CEO and management) throughout the organization. A standard is the lowest level of control that cannot be changed, while a procedure is a sequence of steps. Guidelines are simply a review of how a task can be executed.
Policy [Strategy] Document – contains the general idea, management’s intentions in creating rules to ensure fair treatment, discipline, and compliance, for example, Dress Code Policy, and Internet Policy.
Standard – a set of mandatory rules supporting the policy. It is the level of quality that we want to achieve, for example, the standard of final drawings. Standards have high authority and may include procedures and requirements. A standard is set by the organization, and employees do not have the ability to make changes.
Procedure – a requirement, checklist of items, a series of individual steps that must be followed to achieve the standard. It is created by employees who are experts in a particular field.
Guideline – guidance, advice, and best practices that help achieve a goal, such as showing behavior in a particular situation. They are recommended but not mandatory.
Documentation in the design and construction industry
Each company has its own specifics of project creation: its own styles, tables, and work methodology. Some companies specialize only in one industry and outsource the rest. Some manage the entire project from concept to construction work, so there is not only one solution to how documents such as strategies, standards, procedures, and guidelines should look.
Now that we know the definitions and can organize the relevant information in order, let’s ask ourselves questions that will help us define the company’s goal:
- What is the purpose of creating standards, procedures, and guidelines and what do we want to achieve?
- As a company, what are our standards, for example, for projects – what do our final drawings and models, lists, descriptions, etc., consist of?
- What do we need to establish in order to achieve the standard – what is repeatable and unchanging for each employee?
- What are the guidelines, general advice, and instructions for action to facilitate maintaining the standard?
Once we have answered why, what, and how we need to implement in order to streamline the process, it is worth outlining a team of people who will be responsible for this.
- Who is the documentation addressed to?
- Who will be responsible for the creation and updates of the documentation?
The PSPG documentation should contain concise and practical information. The recipients of the documentation are designers and 3D modeling specialists. This applies to both new and existing employees, industry managers who supervise work, and engineers who are responsible for the quality of information contained in the models. These recipients should also actively participate in the process of updating and creating documentation.
Sometimes, some elements of the standard and procedures (e.g., model naming conventions) may be imposed by the client and may then vary depending on the project. However, the process of creation, order, and organization should be set by the design office or construction company.
The documentation should not be an instruction manual for using a particular program. Such information can be obtained from the software manufacturer’s website or found on YouTube or forums in a very simple way. According to the BIM methodology and the general understanding of this term, we try not to duplicate information, but to use what has already been developed, automate and streamline the design process.
Example of PSPG based on Revit - Autodesk
When it comes to design work, it is worth using an example based on the REVIT program by Autodesk, as many companies in Europe and around the world design Electrical, MEP, Structural, and Architectural installations in this program. The basic PSPG for the REVIT program should include:
REVIT POLICY – the company describes the general goals of the documentation created, e.g.:
- Facilitate work and communication between industries
- Standardize work in the model
- Minimize the possibility of own interpretation of program-project solutions
REVIT STANDARD – presentation of model standards and information contained therein, e.g.:
- Description of a sample model in the program – broken down into parts
- Description of a sample drawing
- Description of a sample arrangement of the main page in the program
- Explanation of the folder structure
REVIT PROCEDURES – the goal is to record the requirements for how to achieve the Standard assumptions, e.g.:
- Description of the template, which is the basis for each project and contains specific lines, fonts, filters, parameters, and tables
- Everything can be found in the XYZ folders divided into various parts – explaining exactly what each folder is for
- Information on naming and creating new folder names, files, central and local models, families, and parameters
- Information on how to correctly export and import files
REVIT GUIDELINE – a file containing advice and best practices for program users:
- Best practices for maintaining order in the program – how to classify views and sheets
- Tips on how to use global, ordinary, and shared parameters
- How to use existing filters
- How to quickly edit families and how to access editing
- Best practices for creating and editing legends and schedules
- Practices and advice on how to use certain attributes
- Tutorials and best “pro tips” can be added to the guidelines.
Practical example – description of creating a wall in 3D program
It is worth noting that 3D programs give us many more possibilities for interpreting the selected path of creating elements than 2D programs. For example, we can create a wall that consists of one part but is divided inside into a plinth, a base, and a cornice, or create three separate walls named plinth, base wall, and cornice.
Each method has its pros and cons. Three separate walls can be problematic when we want to move the wall, and we should remember about two other elements that need to be checked if they are moved automatically or need to be adjusted manually. The program usually helps us with this and informs us about the elements that are “floating”. But as we know, we don’t always have time to check 3D models, for example, if we only provide specific flat 2D drawings for the client. On the other hand, the 3-in-1 wall is for more advanced users and requires more time and analysis in the initial phase, but in the later phase, it facilitates changes.
This is a simple example, but in a large company that works on many projects, details and time matter. It is good to choose one way of creating walls (and other elements such as floors, columns, windows, etc.) and stick to it when modeling. Such information should be included in the Guideline as advice on how to skillfully model to facilitate editing the model. In the procedure, we would describe the name of the wall, which should be defined as, for example, Wall_Plasterboard_10cm.
Summary
The main goal of the PSPG documents is to:
- Assist in the proper and effective implementation of employees into project work and company practices
- Facilitate communication within the team and reduce ambiguity, problematic issues, and errors
- Minimize time and financial losses associated with a lack of agreement, by not reinventing the wheel every time
- Maintain models in the same standard through appropriate procedures and guidelines so that every employee opening a file can easily understand what they see, where they are, and where to find what they need.
BIM and 3D design are already rapidly advancing, and this is just the beginning of introducing new technologies in construction. Construction companies face the difficult task of keeping up with trends and clients’ expectations in a narrowing market with increasing competitiveness. Anything that helps us stand out from the competition is a good bargaining chip because ultimately economic and financial aspects matter most for companies. We save when we implement standards, procedures, and guidelines that will help in daily work and meet the needs of employees. We gain when we eliminate chaos, stress, and anxiety because it does not promote efficiency and creativity, and we aim to create a friendly work environment, reduce costs, and reduce turnover among specialists. We follow the spirit of time and technology, believing that a satisfied and calm employee is a happy and more productive employee.
Let’s look at the IT industry as an inspiration and an example to make it easier for us to keep up with progress and increase work efficiency. Do you have any interesting examples or experiences when PSPG documentation would have been useful in your company? When replacing someone on a project was so difficult or impossible that you had to wait for the person who handled it to come back?
Detailed strategies, standards, procedures, and guidelines based on a simple model of a house will be discussed in upcoming articles! We will take a closer look at the benefits of having documentation in the company that reduces the “Bus Factor” risk.
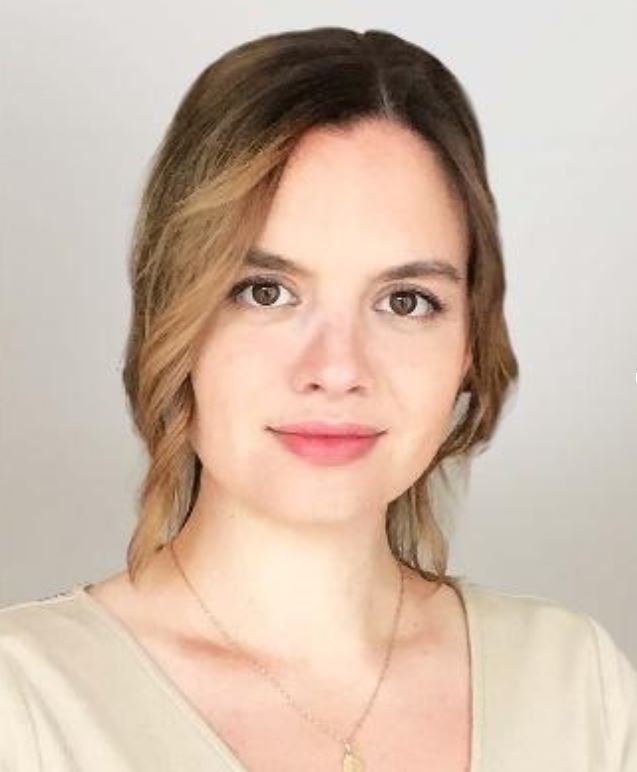